Shell & Tube Heat Exchanger
Heat Exchanger Design, Inc. offers shell and tube exchangers starting at 2" IPS in all TEMA types. We design and fabricate to ASME code and TEMA standards. Our shell and tube line utilizes bare tube (straight and u-tubes), helical low-fin outside, longitudinal fins (inside & outside are available). These exchangers are suitable for a variety of applications and are offered in fixed tube sheets or removable bundles. The surface area ranges from (1) square foot to 40,000 square feet. Pressure range is from full vacuum to over 14,000 PSI (limited by size, material and design condition).
Types and applications of shell & tube heat exchangers:
1. Type U – U-Tube Exchangers: These units are constructed using U shape tubes that are attached to the same tubesheet. This design may be used with A, B, C, N, or D type front end. |
Advantages:
- Tube bundle is removable; therefore mechanical cleaning is possible on the shell side.
- Attachment of tubes to single tubesheet eliminates the need for differential expansion joint.
- This type is suitable for high pressure.
- High degree of protection from leakage is possible.
- Double tubesheet is possible to provide further protection from leakage.
|
Limitations:
- Only chemical tube side cleaning is possible.
- Access to the tubes other that the outside row is limited.
|
For the above reason, this type is recommended for clean process fluids and those subject to chemical removal. |
2. Type L, M, and N – Fixed tubesheets: These units are constructed with the tubesheets integral with the shell. They may be used with A, B, or N Type front head. |
Advantages:
- High degree of protection against contamination of streams.
- Double tubesheet is possible.
- Mechanical tube side cleaning is possible.
|
Limitations:
- Differential expansion is possible only by using expansion joint.
- High pressure application is limited.
- Tube bundle is not removable.
- Shell side mechanical cleaning is not possible.
|
These types are recommended for low and high pressure, and low fouling fluids. |
3. Type W – Externally sealed tubesheets: The shell side and tubeside streams are individually sealed by individual packing and are separated by a lantern ring. This is the lowest cost of the floating head designs and can be used with type A, B, or C front head. |
Advantages:
- Differential expansion between tubes is possible thru the floating head design, therefore eliminates the need for an expansion joint.
- Tube bundle is removable. (Also individual tubes)
- Tube side mechanical cleaning is possible.
- Shell side mechanical cleaning is possible.
|
Limitations:
- Maximum of only two tube side passes is possible.
- The shell and tube side leakage is possible.
- Maximum temperatures of 375 degrees F and maximum pressure of 300 psi limits the usage of these units at higher pressure and temperature.
|
This type is recommended for low pressure, low temperature and non-hazardous fluids. |
4. Type P – outside packed floating head: A skirt attached to the floating tubesheet passes through the back end of the shell. The space between the skirt and the shell is sealed by several layers of packing and packing gland. |
Advantages:
- High pressure on tube side is possible.
- Tube bundle is removable. (Also individual tubes)
- Shell and tube mechanical cleaning is possible.
- More than two tube passes is possible to utilize the allowable pressure drop.
- Packing failure is externally visible under operation.
- Double tubesheet is possible.
- Differential expansion is provided by the packing.
|
Limitations:
- Hazardous material should not be used on the shell side because of the possible leakage.
- Packing will tend to limit shell fluids to temperatures below 300 degrees F and pressure below 150 psi.
|
The above types are recommended for low pressure, low temperature non-hazardous fluids. |
5. Type T – pull through floating heads: The floating tubesheet is designed with a larger diameter than required for the tube array. |
Advantages:
- Tube bundle is removable. (Also individual tubes)
- Differential expansion is provided by the floating head.
- Shell and tube side mechanical cleaning is possible.
- Double tubesheets are possible.
|
Limitations:
- The seal is not externally visible; therefore leakage might be undetected for some time.
- This type will tend to be more expensive than other types.
|
6. Type S – Inside split backing ring: The floating tubesheet is sealed to a floating head cover using a split backing ring and a gasketed surface. |
Advantages:
- High pressure is possible.
- Differential expansion is provided by the floating head.
- Shell and tube mechanical cleaning is possible.
- Tube bundle is removable.
|
Limitations:
- Failure of gasket is not externally visible, therefore leakage might go undetected for sometime.
|
The above type is recommended for high pressure, non-hazardous process fluids. |
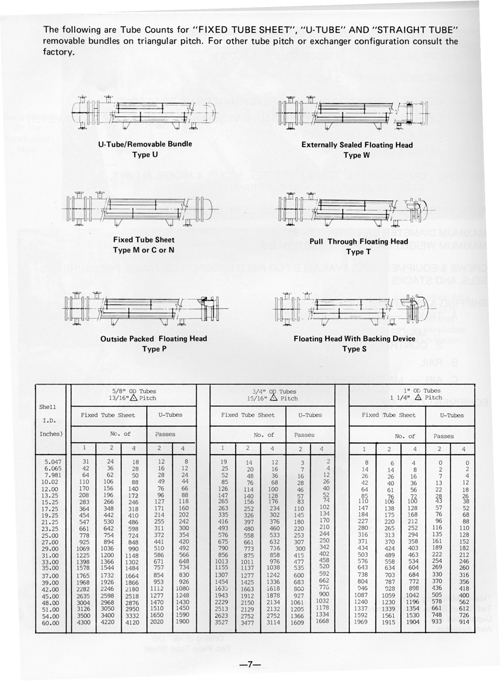
Click on this image for a PDF Printable Document
Fuel Gas Heater for GE turbine
|
High Pressure Shell & Tube for offshore installation
|
Tube Bundle and Insertion
|
View of Tube Bundle Cage with Double Segmental Baffle |
|